Innovation and IT
Deployment of innovative tools is a critical lever to improve Nornickel’s business processes and workplace safety. Nornickel is continuously working to ensure technological sovereignty and developing IT initiatives to support its key business segments.
In 2024, the Company updated its innovation and R&D strategy. Its key strategic priorities include reliability and availability, agility and achieving technological sovereignty.
Strategic goals:
- accelerate decision making
- attract the necessary capabilities
- ensure IT landscape stability during transformation
Key focus areas in innovation
Nornickel relies on innovative technologies, including artificial intelligence (AI) and machine learning (ML), at all stages of its production process — from exploration to smelting — to streamline processes and make its operations safer for people and the environment.
The Company’s goal is not only about research, development, and deployment of promising technologies but also about building the Company’s own R&D capabilities, shaping internal policies, and fostering a culture of high‑tech developments.
The primary contractor for scientific and technical projects for the Company is a dedicated research institute. It is one of Russia’s largest research and engineering centres for mining, concentration, metallurgy, and processing of minerals, with a comprehensive portfolio encompassing the development and production of scientific and technical products. In 2024, the institute secured international patent protection for its proprietary roast‑leach‑electrowin technology in Canada, Finland, Sweden, and Spain.
Ecology and industrial safety
Emissions monitoring
In the reporting year, the development of the core platform for the Axioma predictive emission monitoring system (PEMS) base platform was successfully completed. Developed internally by Nornickel, this innovation offers an alternative to complex and costly automated control systems that rely on sensors and gas analysers.
The core purpose of the technology is to use AI to analyse pollutant emissions from operations by creating a digital twin that continuously pulls data on the status of the production process. The Axioma system can predict emissions based on the current operational load. To achieve this, data from weather stations are used. Predictive modelling of plume trajectory and dispersion enables specialists to adjust process parameters and prevent the spread of harmful substances into urban areas. This solution also supports forecasting the volume and composition of emitted substances as well as tracking relevant environmental indicators as levels of equipment utilisation change. The impact of emission reductions on meeting production targets for finished products is also monitored.
In late 2024, the system was successfully tested at Nadezhda Metallurgical Plant. Experts evaluated the consistency of results from mathematical modelling, accredited laboratory sample analyses, and instrumental readings from certified gas analysis equipment. The tests were conducted in accordance with metrological standards, with a representative of the Mendeleev All‑Russian Institute for Metrology (VNIIM) in attendance.
Axioma stands out as a strategically important and high‑priority project in Nornickel’s portfolio. The Axioma system has attracted significant interest from other leading Russian companies after being showcased at numerous exhibitions and forums.
Project awards:
- Diploma from the BRICS Solutions Awards in the Climate and Environmental Technologies category
- Award for the Best Project Implemented in the Russian Arctic Zone at the 5th Reliable Partner — Ecology national competition of the best local environmental protection practices
Rock mineralisation
In the course of mining, rock is extracted from under the ground and sent to concentrators, where grinding takes place and valuable components are separated from gangue. Gangue is a byproduct of the concentration process (tailings). After that, tailings undergo special treatment and are sent to tailing dumps, where they are distributed across their surface. During prolonged exposure to air, minerals contained in tailings react with carbon dioxide to form stable secondary carbonates, which remain in the tailing dumps. Thus, conditions are created for carbon dioxide capture, or natural mineralisation.
The Company enables conditions under which tailings can capture between 4.5 and 17.9 kg of CO2 per tonne through natural chemical processes, depending on the mineral composition of the gangue. Analysis of natural mineralisation data from the past four years indicates an annual CO2 removal rate of approximately 350 kt. The Company developed a methodology for estimating and accounting for the CO2 absorption capacity of tailings. This capacity was independently audited and verified, and is now factored into greenhouse gas emissions and removals calculations.
Video analytics
To maintain a safety culture at its operations, Nornickel actively adopts solutions that use AI‑enabled video analytics. The Company operates a proprietary solution to monitor the use of personal protective equipment (PPE) by operational staff. The AI‑enabled solution continuously monitors workwear usage on the shop floor, including safety helmets with chin straps buckled up, safety goggles, and other protective equipment. Specialists also train the system to monitor and record the use of a safety harness when working at height. If an employee violates the rules for using personal protective equipment, the system will generate a violation card and send it to the line manager, who will review each case and make a decision. The card is then submitted to a coordinator from the Health and Safety Department for final review.
In 2024, the system’s incident detection capabilities were expanded to include additional safety hazards: working at height, entering hazardous areas around active equipment, and the unauthorised transport of people using machinery not intended for that purpose.
Nornickel’s engineering team also developed a mobile computer vision system for monitoring compliance with industrial safety regulations and supporting various work processes in areas where fixed surveillance cameras and communications channels are unavailable. Pilot tests are scheduled for 2025.
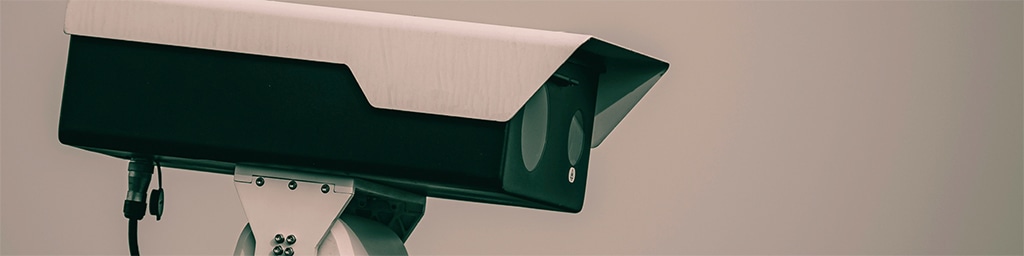
Personnel positioning system at mines
In 2024, the implementation of a precise personnel positioning system was completed at Norilsk site mines. The project is aimed at enhancing the safety of employees working in the hazardous operational environment of the mine. A collision avoidance system was implemented to alert the operator of potentially hazardous proximity to pedestrians and other vehicles. Subsequent functionality development included the design and implementation of an automatic braking and stopping system for self‑propelled vehicles, enabling the vehicle to decelerate or stop autonomously upon detecting a pedestrian in close proximity.
The system enables emergency notification of personnel, helps determine their location, and reduces response time for rescue services during emergencies. The solution includes features such as immobility detection, alerts for hazardous proximity to vehicles, access control for hazardous areas, and other options aimed at improving industrial safety.
Further project development is planned for 2025, including the creation of functionality for managing safe routes for personnel movement and a mobile solution for mining supervisors, designed to improve the speed of production process management without involving the mining dispatcher.
Transport planning and management system
The SPRUT system is being implemented to automate transport management processes. It operates as a single, centralised solution for managing transport operations in industrial settings. The system collects data from onboard equipment and uses this information to optimise traffic flow management. In addition, SPRUT automates transport‑related document workflows and serves as a platform for communication between clients, internal contractors, carriers, and supervisory authorities. At the initial stage, the SPRUT system is designed to manage and monitor road transport operations. Further development will extend its capabilities to cover the planning and tracking of rail and water transport. Looking ahead, the solution will support the development of multimodal supply chains.
Benefits of the SPRUT system:
- Enhanced driver safety and reduced road accident rates
- Lower risk of violations and property damage during transport service delivery
- Calculation across various types of driver remuneration based on actual work performed
In 2024, the development of the system’s core modules was completed, functional testing was carried out, and compliance with customer requirements was confirmed. The SPRUT system is scheduled for commercial deployment in December 2025.
Project awards: the SPRUT system received the 13th ComNews Award for the Best Solution for Transport Service Planning and Transport Management.
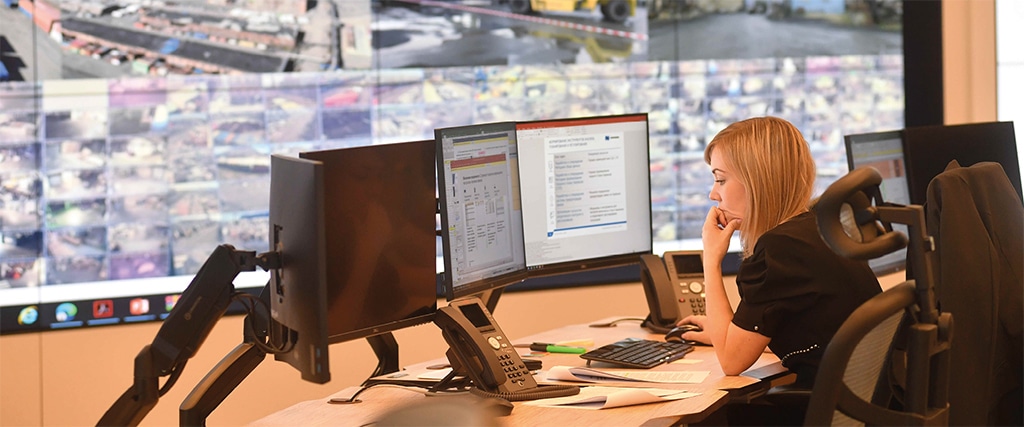
NoRiskNN app
The NoRiskNN mobile application was developed to provide an alternative channel for communicating health and safety (H&S) concerns at the Company’s operational sites. It enables employees to enter information about identified issues directly into the mobile app, allowing any staff member to report risks or potential incidents. Submitted reports are then escalated to coordinators and responsible personnel for resolution. The application streamlines the risk identification process and reduces response times.
Analysis of feedback received during the pilot deployment of the NoRiskNN application highlighted several key suggestions for system enhancement: the introduction of push notifications, the development of a competitive rating system to incentivise risk identification, and improved messaging functionality allowing users to attach photographs to their reports.
The commercial launch of the mobile application is scheduled for 2025.
Enhancing production technology
Geological data analysis
The Company continues a major project to develop and deploy an automated mining and geological data processing and analysis system. The project aims to develop a single digital platform that enables end‑to‑end automation of key business processes in mining operations, including exploration, drilling, sampling, core management, rock quality control, mine planning, design, and mineral extraction activities, ground support, geological and surveying calculations, and reserve tracking. The MinePRO system by Russian developer OT‑OIL was selected for the project and is currently being adapted to meet Nornickel’s specifications.
In 2024, functionality was implemented to enable the recording of mine planning and design data and the management of mine surveying calculations.
Plans are in place to introduce functionality for automating the planning and execution of geological exploration activities, geological modelling and calculations, and mineral reserve tracking.
MinePRO will secure the quality, availability, and accuracy of production data across all levels of the Company, enabling timely and effective management decision making.
Modelling underground blasting
In 2023, the Company launched a project to model underground drilling, aimed at reducing rock dilution with waste rock and concrete during drilling and cleaning as well as cutting drilling and blasting costs.
Using modern software to model upcoming drilling and blasting operations — while accounting for the patterns and interrelationships of rock mass strength properties — enables highly accurate predictions of blasting outcomes and rock fragmentation quality. Blast simulation using numerical methods enables the effective optimisation of target drilling and blasting patterns. It also allows for the simulation and subsequent refinement of blasting performance under actual mining conditions.
In 2024, the initial software adaptation for the main rock types present at the Komsomolsky Mine was completed. Empirical data from test stopes were collected to support the fine‑tuning of simulation coefficients.
The software’s simulation coefficients are expected to be finalised by the end of the first quarter 2025. This will be followed by on‑site pilot tests at the mine, including simulated cleanup drilling projects and controlled blasting trials, to validate the project’s target metrics and support scaling decisions.
Optimising refining processes
In 2024, a project was launched at the refining shop of the Kola site aimed at reducing secondary metal content in concentrates. The project includes automated control of reagent consumption, pulp levels within the flotation sections, and irrigation water supply. As a result, secondary metal content has been reduced by more than 10%.
To date, a flotation control model has been developed, a data‑lake–based solution has been deployed and tested, and a server has been installed and configured within the refining shop. Completion of the pilot phase is expected in the first half of 2025, followed by the transition to commercial operation in the latter half of the year.
In 2024, Nornickel implemented a new precious metal recovery process for converter matte at the Kola site’s refining shop. The new system minimises precious metal losses, thereby enhancing overall production efficiency.
The process for recovering precious metals from crushed converter matte was integrated into the magnetic separation stage of the converter matte separation section. It facilitates the extraction of precious metals from intermediate products during nickel production.
Precious metal recovery from nickel concentrate had previously taken place at this site. With the introduction of a new flow distribution system, it is now also possible to recover precious metals from crushed converter matte.
The engineering solution behind the system was implemented by leveraging the section’s existing capacity. The process is as follows: the converter matte undergoes pre‑treatment — milled in one of the workshop’s ball mills — and is then fed as a pulp to magnetic separation. At this stage, the material is separated: the magnetic fraction, containing precious metals, is directed to the flotation section, while the non‑magnetic fraction, comprising depleted matte, is filtered and packaged into containers for subsequent shipment.
Previously transferred to partners for further processing, the precious metals contained in the converter matte are now retained within the production chain. This enables more effective delivery of the production programme.
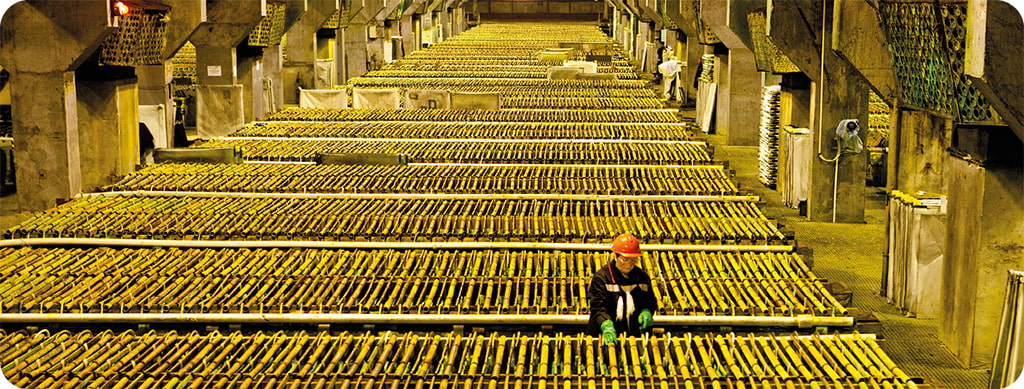
Optimising concentration processes
The Company continued its research on ionometric mapping and optimisation of pulp ionic content during the flotation of copper‑nickel ores at its concentrators. Research showed that ion‑selective electrodes can effectively control the consumption of specific reagents, resulting in improved concentrate quality, increased metal recovery into concentrate, and reduced reagent consumption. The laboratory testing phase was completed in 2024. Pilot tests are scheduled for 2025, after which the project to integrate ion‑selective electrodes for monitoring and controlling concentrator processes may move into the implementation phase. The initiative is expected to improve the recovery of nickel, copper, and PGMs.
At Norilsk Concentrator, ongoing research and development is focused on optimizing PGM recovery through gravity separation methods. A process survey at the concentrator resulted in recommendations identifying potential areas for improvement. The second phase of the research will involve comprehensive laboratory testing to validate these recommendations ahead of pilot trials scheduled for 2025.
Increasing copper recovery in the Trans‑Baikal Division
Initiated in 2023, the project aims to improve copper recovery while maintaining the quality of copper‑gold concentrate.
An optimisation‑based control algorithm for flotation was successfully developed at Bystrinsky GOK, covering all stages of the process. Automated control was implemented for air flow, pulp levels in flotation cells, and the dosing of specific reagents. To enhance the quality of input data, a computer vision algorithm was also developed to supply the system with the information required for effective process control.
In 2024, the solution was transitioned to continuous operation.
Throughout 2025, a comprehensive analysis will be carried out to evaluate the algorithm’s stability and determine the project’s economic potential. Efforts are currently underway to transition the solution to commercial operation.
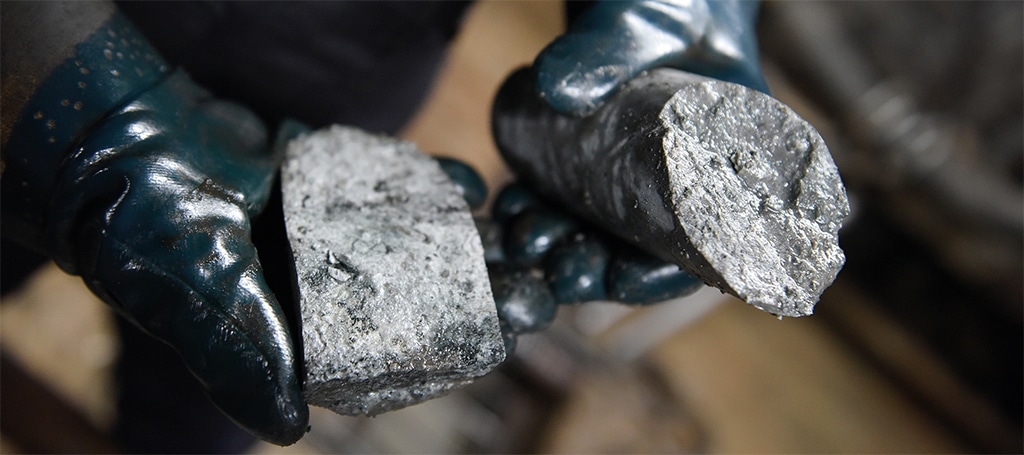
High‑tech products
Palladium Centre
The Centre’s portfolio currently comprises over 25 new palladium‑based products across three distinct application areas — greentech, high‑tech materials, and traditional uses — each at a different stage of development.
In 2024, extensive pilot‑ and industrial‑scale testing was conducted to evaluate new materials for hydrogen energy systems, including catalysts for electrolysers, membranes for ultra‑pure hydrogen production, and fuel cell catalysts. The first commercial deliveries of these materials are expected in 2025. In the reporting year, industrial tests were successfully completed, and the first commercial batch of new palladium‑based anodes for water disinfection via electrolysis was produced. Furthermore, industrial testing of glass fibre bushings with palladium‑based current leads was successfully completed. Product refinement is planned for 2025, with the integration of palladium into the alloy composition.
Also in 2025, the Company intends to complete fundamental research in the area of electric transport, aimed at integrating new palladium catalysts into lithium‑sulphur batteries to extend their lifespan and increase power output. Preliminary estimates suggest that replacing lithium‑ion batteries with lithium‑sulphur batteries incorporating palladium catalysts could multiply the driving range of electric vehicles several times over.
In the long term, the Company aims to bring over 100 new palladium‑based materials to market, which, according to internal estimates, could generate at least 40 to 50 tonnes of new palladium demand by 2030.
Battery materials
In September 2024, Nornickel announced the establishment of its Battery Technology Centre in Saint Petersburg. The project is aimed at advancing the Company’s technological capabilities in the promising field of nickel‑containing cathode active materials — a key component of advanced battery systems.
The new centre will focus on the development and research of battery materials using state‑of‑the‑art process equipment unique in Russia, enabling the full cycle of synthesis and testing under specialised conditions.
In 2024, Nornickel’s R&D centre produced the first samples of cathode materials for NCM 811+ chemistry, with further research planned to develop new products.
Metal powders
Powder metallurgy is a cost‑effective alternative to traditional machining of metal parts. It enables the production of items with unique properties, significantly improves metal use efficiency, and enhances the competitiveness of the final product.
In 2024, the Company successfully developed and produced several prototypes of metal powders derived from nickel‑ and cobalt‑based heat‑resistant alloys. These powders exhibit spherical morphology and possess specific technological properties that make them suitable for a wide range of additive manufacturing technologies, including 3D printing, metal injection moulding, coating deposition, and hot isostatic pressing. This, in turn, enables the production of high‑tech components with complex geometries for use in the aerospace, aviation, energy, and medical industries. The powder prototypes developed by Nornickel were tested by several leading Chinese manufacturers of additive manufacturing equipment, receiving positive feedback supported by formal quality certifications.
Enhancing corporate business processes
Data lake ecosystem
One of the core components of the corporate digital landscape is the data lake — a scalable platform for digitising technological and business processes. It is designed to store and analyse data across the entire Group while driving synergies by enriching data in external systems with new information. Integration data flows from Nornickel’s core production sites have already been incorporated into the ecosystem.
A proprietary framework has been developed to streamline the integration and processing of equipment sensor data, leveraging advanced open‑source solutions. The existing tools support the integration of machine‑learning models, generation of analytical reports, creating custom calculations, and running basic quality checks on metrics — without the need to develop additional standalone components.
The data lake solution is built using domestically produced Russian products and open‑source systems and consists of four primary components:
- Data Platform — storage and processing of big data;
- Containerised environment — for deploying MLMachine learning. applications and Industrial ML instances;
- ML Platform (ML environment) — a corporate platform for developing and integrating machine learning (ML) models into operational processes;
- ML Clusters — a geographically distributed infrastructure for the deployment of ML solutions at production sites.
The Data Platform and ML Platform were officially launched into commercial operation in 2024. The data lake is now integrated with the main manufacturing execution systems (MES) Information systems designed to manage production processes at the enterprise level. used at Nornickel’s production sites.
The ML clusters at the Kola site and Talnakh Concentrator are scheduled to enter commercial operation in 2025. The ML cluster at the Kola site will operate as a megacluster, enabling the simultaneous deployment of innovative solutions across multiple concentrators. The launch of the ML cluster at Norilsk Concentrator is scheduled for 2026.
These ML clusters are primarily intended to achieve two goals:
- Accelerating the deployment of digital production projects by removing the need for iterative design and deployment of integration infrastructure;
- Reducing the analytical load on production control and dispatch systems.
Integrated document management
Further development of the Integrated Document Management programme continued in 2024. The initiative is aimed at holistically enhancing the quality, speed, agility, and technological maturity of business process documentation.
As a result of project and operational activities during the year, all Group enterprises completed the transition to legally binding electronic document management (EDM).
The volume of automated routine tasks related to accounts payable processing increased.
Compliance with legal requirements for machine‑readable powers of attorney within the EDM system was achieved through the implementation of a solution for issuing and monitoring the status of such documents, thereby ensuring the legal validity of electronic signatures applied to documents.
The scope of electronically processed contractual documentation was expanded, and digital signing of work/service orders was introduced. Since the start of the pilot operation, two Group enterprises have fully transitioned their work/service order processing to an electronic format.
The practices developed through this initiative also enabled the effective use of EDM functionality for tax monitoring and ensured compliance with document submission requirements established by the Federal Tax Service of Russia.
Supernika mobile app
In 2023, Nornickel developed and deployed Supernika, Russia’s first corporate super app. The platform integrates a wide range of digital services for both employees and management, including an employee personal account, a messaging tool, and a unified media centre. It provides all employees with 24/7 mobile access to all available corporate resources directly from their mobile phones.
In under a year since production deployment, the Supernika platform was adopted by over 80 thousand users across the Company.
New digital services are now being designed with native integration into Supernika in mind. In 2024, the app was enhanced with a new Personal Protective Equipment (PPE) service, enabling employees to fully manage and access PPE‑related information.
HR electronic document management
Preparations are underway for the pilot deployment of Nornickel’s HR electronic document management system (HR EDMS). In 2024, all necessary configurations were completed on the domestic Directum RX platform, and preparatory work for launch at the corporate Head Office was finalised. The HR EDMS will minimise the use of paper‑based documents, increase the productivity of HR staff supporting personnel processes, enable the transformation and technological unification of business process documentation, and provide the ability to forecast and respond quickly to internal and external changes affecting document flows in HR and social business processes.
Throughout 2024, Nornickel significantly expanded the functionality of its core corporate systems and services for employees and management. These improvements are expected to optimise and substantially enhance the efficiency of internal business processes, including HR administration, the Golden Rules of Safety, training, employee evaluation, and other key tasks.
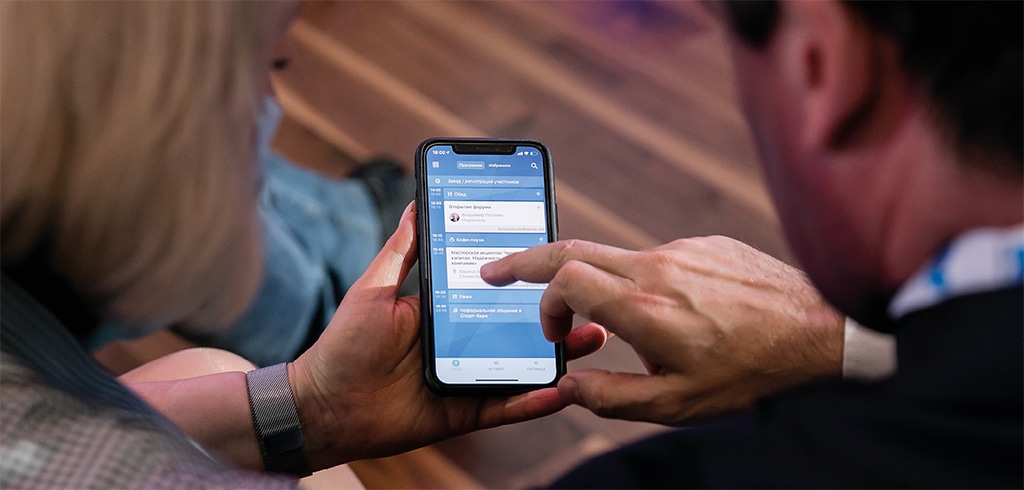