Industrial safety
Contribution to the UN SDGs
Key strategic objectives in health and safety for 2023–2025:
- Achieve the industry average injury rate
- Achieve zero fatalities
Strategic goals
Zero fatalities
The Company has a zero-tolerance policy for work-related fatalities
No major accidents at production sites
Measures to prevent accidents at the Company’s facilities and the associated negative impact on local communities in operating regions or operational performance
Steady reduction of health and safety risks to a tolerable level
Safe working conditions for employees and mitigation of ore mining and processing risks
In the past year, the Company was strongly focused on enhancements to mine safety systems with the launch of the Critical Risk Management project.
A three‑tiered safety barrier system was introduced to minimise the risks of severe and fatal accidents. The system is currently in the pilot deployment phase across all Company mines. Moving forward, the safety barriers will be integrated into the production control system, and enhancing its effectiveness remains a key strategic challenge for the Company in 2025.
In 2024, a comprehensive employee survey was conducted to evaluate perceptions of health and safety. Based on the results, several initiatives were developed and implemented – the most effective, such as Detecting Unsafe Activities and the On‑Site Training Programme for H&S Staff, are planned for further development and scaling in 2025.
Additionally, the Company launched the Life and Safety – Work Environment project, establishing a unified H&S communications system via a dedicated Telegram channel.
Management system and KPIs
Key performance indicators
Up to 30% weighting in team KPIs of all Group employees
Goal:
Deliver on the H&S action plan and reduce FIFR by 50% or more from a 2021 baseline
Up to 40% weighting in individual KPIs of production site managers
Goal:
100% implementation of the H&S action plan within the established timeframe
Within the Group’s team KPIs, 30% of the weighting is assigned to the implementation of the action plan designed to enhance safety culture and reduce work‑related fatalities. These initiatives are directly overseen by senior management, including members of the Management Board. When evaluating performance against this KPI, an adjustment factor based on the current FIFR Fatal injury frequency rate, the number of fatalities per million hours worked. rate is applied. The FIFR reduction target is based on achieving an annual decrease from a 2021 baseline, with a goal of at least a 50% reduction by end‑2024.
Production site managers are personally responsible for the health and safety of each of their subordinates. Injury and industrial safety metrics weigh up to 40% in their individual KPIs. The target is to achieve 100% implementation of the H&S action plan within the established timeframe.
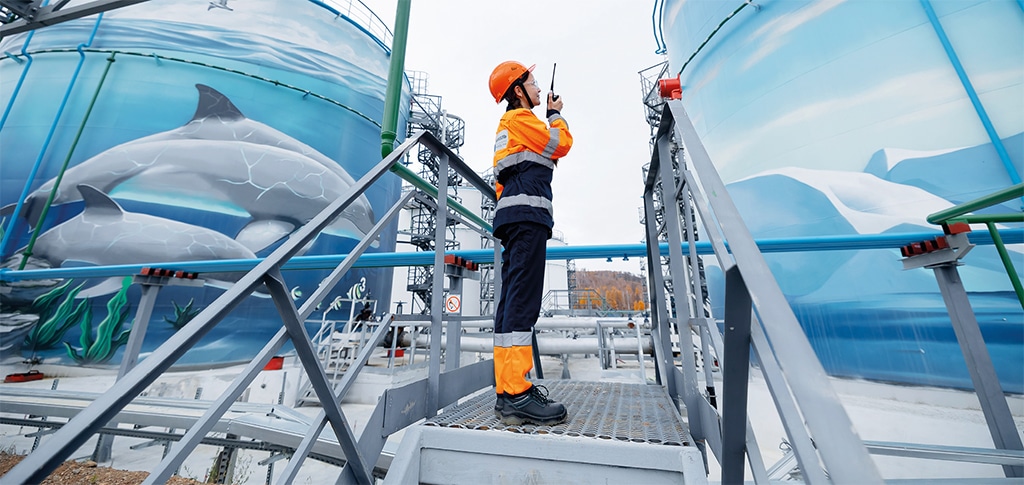
Industrial safety matters are overseen by the Audit Committee of the Board of Directors. The Committee reviews quarterly management reports on industrial safety performance and is briefed on the causes of accidents, the measures taken to prevent similar incidents in the future, and any disciplinary actions taken against those responsible.
The Company also has a Health, Safety, and Environment Committee, chaired by the Senior Vice President – Chief Operating Officer. Its main objectives are to improve performance and accountability in health and safety. The Committee holds quarterly meetings at the Group’s production sites.
Industrial safety audits
The Company conducts regular audits of its occupational safety management system. In 2024, Nornickel successfully completed the audit and renewed its certificate of conformity. The certification body, Bureau Veritas Certification, described the Company’s management system as mature and well‑established and confirmed that the corporate systems of Nornickel’s audited enterprises met the relevant requirements of the applicable standard. The Company’s strengths cited by the auditor include the ongoing safety culture development project; the use of IT solutions and risk‑based approach tools; contractor management practices; and a strong focus on continuous improvement of the health and safety management system.
At the end of 2024, 53% By average headcount. of Group companies were certified to ISO 45001:2018 for occupational health and safety.
In 2024, new auditing techniques were developed and refined, including:
- maintenance audits, which assess an enterprise’s readiness to carry out maintenance activities and the effectiveness of supervising safe work practices
- comprehensive health and safety audits, aimed at identifying systemic gaps, uncovering root causes, and proposing corrective actions
- targeted audits at mine sites (focusing on mining operations), incorporating the three‑tiered safety barrier model – technical, procedural, and behavioural.
Work‑related injuries
In 2024, the Company continued implementing its Building Risk‑Based Thinking Skills project, aimed at revising the health and safety incident reporting process to enhance transparency and improve the accuracy of incident classification. As a result, the Company achieved faster response times and expanded its capacity for further in‑depth analysis of workplace incidents. The process for incident investigation and root cause analysis was also significantly revised, opening up additional opportunities for proactive incident prevention in the future.
The lost time injury frequency rate (LTIFR) decreased to 0.64 in 2024, while the fatal injury frequency rate (FIFR) reached a historic low of 0.025.
Tragically, three fatal workplace accidents were recorded at the Company in 2024. Each accident was thoroughly investigated, with reports submitted to the Board of Directors and action plans developed to address the root causes. The Company continues to improve the quality of its incident investigations and is reshaping its occupational safety communications with employees.
Indicators | 2020 | 2021 | 2022 | 2023 | 2024 |
---|---|---|---|---|---|
Falls from height | 0 | 1 | 1 | 0 | 0 |
Falling objects | 2 | 0 | 0 | 0 | 0 |
Moving objects/parts | 1 | 3 | 0 | 0 | 0 |
Rock fall | 2 | 2 | 2 | 0 | 0 |
Underground transport | 0 | 0 | 0 | 3 | 3 |
Electrocution | 3 | 1 | 0 | 0 | 0 |
Collapse of structures | 0 | 0 | 0 | 2 | 0 |
Explosion | 0 | 0 | 0 | 0 | 0 |
Other | 1 | 4 | 1 | 0 | 0 |
Total | 9 | 11 | 4 | 5 | 3 |
Following the investigation into an incident where an employee was pinned by a load‑haul‑dump (LHD) machine, the Company decided to equip all LHDs with the Interlock system, which automatically activates the parking brake after three seconds of inactivity on both the accelerator and brake pedals. Additionally, video recording devices were installed in LHD cabs to enable monitoring of operator behaviour. A list of critical faults that prohibit machinery from being operated has been established, along with a procedure for equipment acceptance following repairs.
To address the root causes of another incident in which an employee was pinned between a pipeline and a mine wall, the Company enhanced the functionality of the positioning system to enable monitoring of self‑propelled diesel equipment while stationary during shift breaks. The standard pipeline fixation design was also updated, providing detailed guidance on approved securing methods. All designated vehicle access points for passenger boarding and exiting were brought into compliance with established standard requirements.
Following the investigation into the incident involving a dump truck striking a pipeline, the mine’s production control processes were overhauled across all levels of management. The requirements for planning the installation and dismantling of process pipelines, as well as the inspection and acceptance of completed work, were revised.
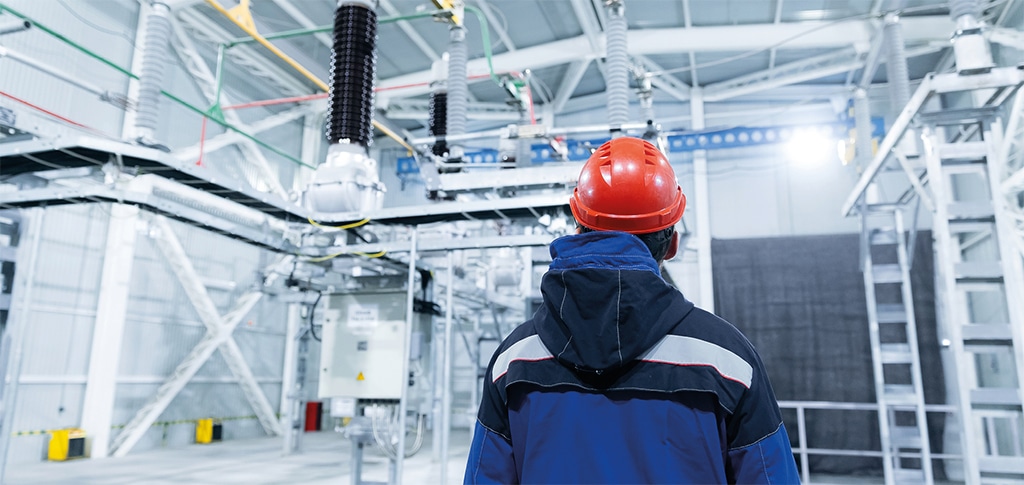
Contractor safety
Indicators | 2020 | 2021 | 2022 | 2023 | 2024 |
---|---|---|---|---|---|
Work‑related injuries, including: | 18 | 30 | 46 | 32 | 31 |
Lost‑time injuries | 15 | 28 | 42 | 25 | 30 |
Fatal injuries | 3 | 2 | 4 | 7 | 1 |
LTIFR | – | – | – | – | 0.52 |
FIFR | – | – | – | – | 0.017 |
The Company’s procedural documents on industrial safety – including regulations, policies, corporate standards, and the Golden Rules of Safety – also apply to contractor employees.
When engaging contractors, the primary focus in health and safety is on preventing fatal incidents and ensuring compliance with industrial safety requirements.
In 2024, the Company launched a system for collecting injury statistics, including the calculation of contractor‑specific LTIFR and FIFR.
All tasks performed by contractors in high‑hazard environments are carried out in accordance with corporate safety standards. Work permits must include occupational safety requirements to be followed during both the planning and execution of tasks. Compliance with these requirements is monitored on every shift. Prior to the commencement of any work, contractor employees are required to receive induction and targeted briefings on occupational health, including safety measures.
Contractor representatives participate in both regular joint safety inspections and H&S committee meetings held at Nornickel sites. If contractors fail to comply with safety requirements, penalties are imposed.
To foster a culture where safety is a shared value among all stakeholders, Nornickel holds an annual forum with major contractors to discuss relevant case studies and safety challenges. These discussions are supported by training sessions delivered by the Company’s internal safety coaches. The forum reinforced the understanding that safety is a collective responsibility, not solely that of the customer.
In addition, Nornickel regularly organises contractor training sessions on Dynamic Risk Assessment and Behavioural Safety Audits.
Safety culture
The Company continuously improves its H&S system elements. These changes cover all production units of the Company – from mining ore to making metals.
Indicators | 2020 | 2021 | 2022 | 2023 | 2024 |
---|---|---|---|---|---|
Health and safety expenses (RUB mln), including: | 9,724 | 12,728 | 21,697 | 17,505 | 19,784 |
Expenses per employee (RUB thousand) | 136 | 173 | 272 | 218 | 256 |
To maintain a high level of employee awareness regarding safety measures, the Company regularly develops and updates its guides, videos, presentations, and other visuals highlighting key safety measures for protecting life and health in various situations or when performing specific tasks. All Company employees have access to occupational health information.
For example, in 2024, Nornickel focused on the following key initiatives:
- Changing the communication format – with an emphasis on clear, engaging examples related to health and safety
- Implementing proprietary digital solutions to prevent accidents
- Introducing a new audit format aimed at identifying systemic gaps
- Sharing and replicating lessons learned from incident investigations
The Company has a formal procedure in place that allows employees to refuse work if they are exposed to risk. Such refusal does not result in any disciplinary action against the employee. Each employee has the option to anonymously contact the Corporate Trust Line in case of complaints or suggestions. Additionally, employees are encouraged to ask questions and receive feedback from managers at all levels during working meetings, huddles, and similar events.
Emergency preparedness
In line with legal requirements, Nornickel maintains a constant state of emergency preparedness across all units, including for emergency containment and response. This is particularly critical, as the Company operates more than 300 hazardous facilities that use hazardous substances in their production processes.
Emergency preparedness procedures
Every enterprise has in place on‑site emergency response plans
Employees undergo training on emergency response actions, and drills are conducted
Contracts with professional emergency rescue services and organisations are maintained
Reserves are in place to support emergency response at hazardous facilities
Mine rescue teams have been established and take regular training under conditions as close to real emergencies as possible
Emergency surveillance, alert, communication, and response support systems have been installed across facilities
Monitoring of violations
Nornickel has developed and operates a multitiered H&S monitoring system, which includes ad hoc, targeted, and comprehensive H&S inspections. The Company’s incident reporting procedure and incident classification system enable prompt response to incidents and enhance the quality of subsequent analysis.
In 2024, the Company implemented a new tool that enables centralised incident logging in a unified database, efficient tracking of investigation progress and statuses, secure storage of investigation results, and more effective information sharing across units.
In addition, the Company conducts behavioural safety audits. As a result of prevention and control efforts, more than 8 thousand industrial safety violations were identified, with the responsible employees held accountable, including through partial or full withholding of bonuses.
Employee training
The Company is committed to ensuring that its employees have the necessary knowledge, skills, and competencies to perform their duties safely and responsibly.
Training begins immediately after hiring, starting with a health and safety induction, followed by on‑the‑job briefings. Thereafter, briefings and training sessions are held regularly in line with corporate programmes and the specific nature of each role. All Group employees regularly take online industrial safety trainings followed by tests. Interactive training courses have also been developed for employees in core operational roles.
Indicators | 2020 | 2021 | 2022 | 2023 | 2024 |
---|---|---|---|---|---|
Number of employees trained | 34,040 | 38,253 | 51,520 | 57,114 | 55,427 |
Percentage of employees trained | 47 | 52 | 66 | 72 | 70 |
Number of trainings conducted | – | – | 707 | 4,262 | 4,045 |
A project to establish a train‑the‑trainer programme for safety culture was launched in September 2022. Its training programmes are updated annually. In 2024, a total of 4,045 training sessions were conducted, with more than 55 thousand employees trained under the project. In addition, the trainers delivered training to over 1 thousand contractor employees and 510 students as part of the initiative.
Protection against health hazards
The Company protects employees from workplace health hazards by providing collective and personal protective equipment, introducing effective work and rest schedules, and improving workplace amenities. All employees have a mandatory meal break during their shifts.
Employees exposed to hazardous substances undergo special medical examinations at occupational pathology centres. Personnel working in contaminated environments are provided free of charge with wash‑off and decontaminating agents. Employees operating in hazardous or highly hazardous conditions are entitled to free preventive nutrition, milk, or equivalent food products.
Prevention of occupational diseases
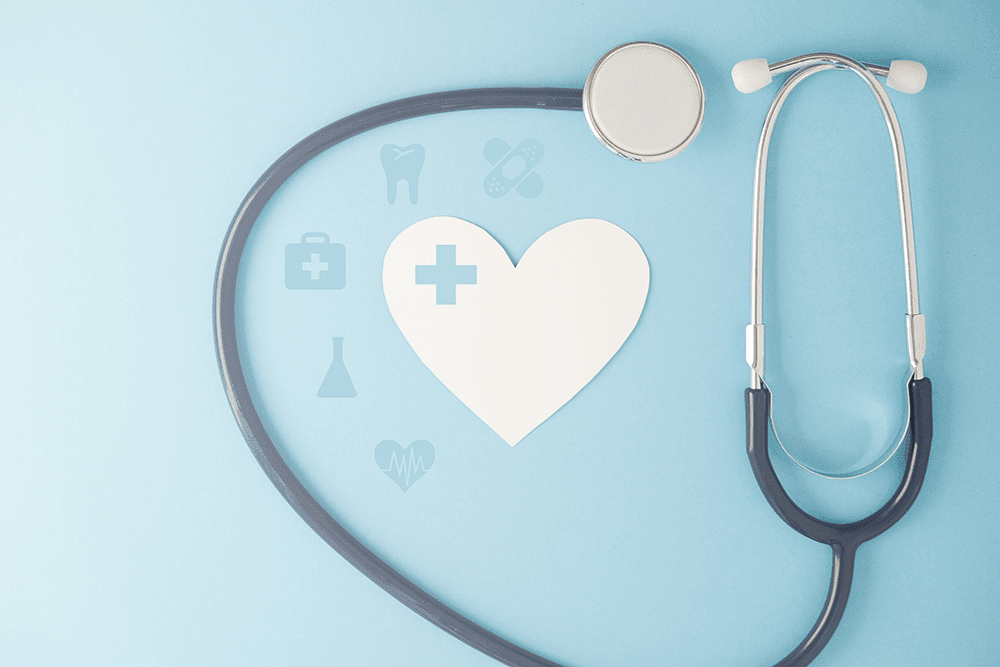
Most Company employees reside in the Norilsk Industrial District. To minimise the risk of occupational diseases, Nornickel operates the Sulphur Project aimed at reducing sulphur dioxide emissions, implements effective healthcare measures that consider both workplace and personal risk factors, and encourages healthy lifestyles.
Regular health monitoring of employees is a key element in preventing occupational diseases. All employees undergo mandatory pre‑employment and regular medical examinations at the Company’s expense throughout the course of their employment. On‑site medical aid posts operate at production facilities to conduct pre‑shift health checks and provide medical assistance upon request.